What is Porosity in Welding: Vital Tips for Achieving Flawless Welds
What is Porosity in Welding: Vital Tips for Achieving Flawless Welds
Blog Article
Porosity in Welding: Identifying Common Issues and Implementing Ideal Practices for Avoidance
Porosity in welding is a prevalent concern that typically goes unnoticed up until it creates substantial troubles with the integrity of welds. In this discussion, we will certainly discover the crucial factors contributing to porosity formation, examine its damaging impacts on weld performance, and discuss the best practices that can be taken on to lessen porosity incident in welding procedures.
Usual Causes of Porosity
Another frequent perpetrator behind porosity is the visibility of impurities externally of the base steel, such as oil, oil, or corrosion. When these contaminants are not successfully eliminated before welding, they can vaporize and end up being caught in the weld, causing flaws. In addition, utilizing dirty or wet filler materials can present contaminations into the weld, contributing to porosity issues. To reduce these common reasons of porosity, complete cleaning of base metals, proper shielding gas option, and adherence to optimum welding specifications are vital methods in accomplishing top notch, porosity-free welds.
Effect of Porosity on Weld Top Quality

The visibility of porosity in welding can significantly endanger the structural stability and mechanical homes of welded joints. Porosity creates gaps within the weld steel, deteriorating its total stamina and load-bearing capability.
Welds with high porosity levels often tend to exhibit lower influence stamina and reduced ability to warp plastically before fracturing. Porosity can impede the weld's capacity to successfully transfer pressures, leading to premature weld failing and potential security risks in crucial frameworks.
Finest Practices for Porosity Prevention
To boost the architectural stability and quality of bonded joints, what certain measures can be carried out to reduce the occurrence of porosity during the welding procedure? find Using the correct welding method for the certain product being bonded, such as readjusting the welding angle and gun setting, can further avoid porosity. Regular inspection of welds and prompt removal of any issues determined throughout the welding procedure are important methods to stop porosity and produce top quality welds.
Value of Correct Welding Techniques
Carrying out correct welding strategies is vital in guaranteeing the architectural stability and high quality of bonded joints, constructing upon the foundation of reliable porosity prevention steps. Welding strategies straight influence the overall toughness and sturdiness of the bonded structure. One vital facet of proper welding strategies is keeping the proper warmth input. Too much warm can result in increased porosity as a result of the entrapment of gases in the weld pool. Conversely, inadequate warmth might result in incomplete discover here blend, producing possible weak factors in the joint. Additionally, utilizing the proper welding specifications, such as voltage, existing, and take a trip speed, is essential for accomplishing sound welds with marginal porosity.
Additionally, the choice of welding process, whether it be MIG, TIG, or stick welding, should align with the certain needs of the project to ensure optimum results. Proper cleansing and prep work of the base steel, along with picking the right filler product, are also crucial elements of proficient welding methods. By sticking to these ideal techniques, welders can decrease the threat of porosity development and produce top quality, structurally audio welds.
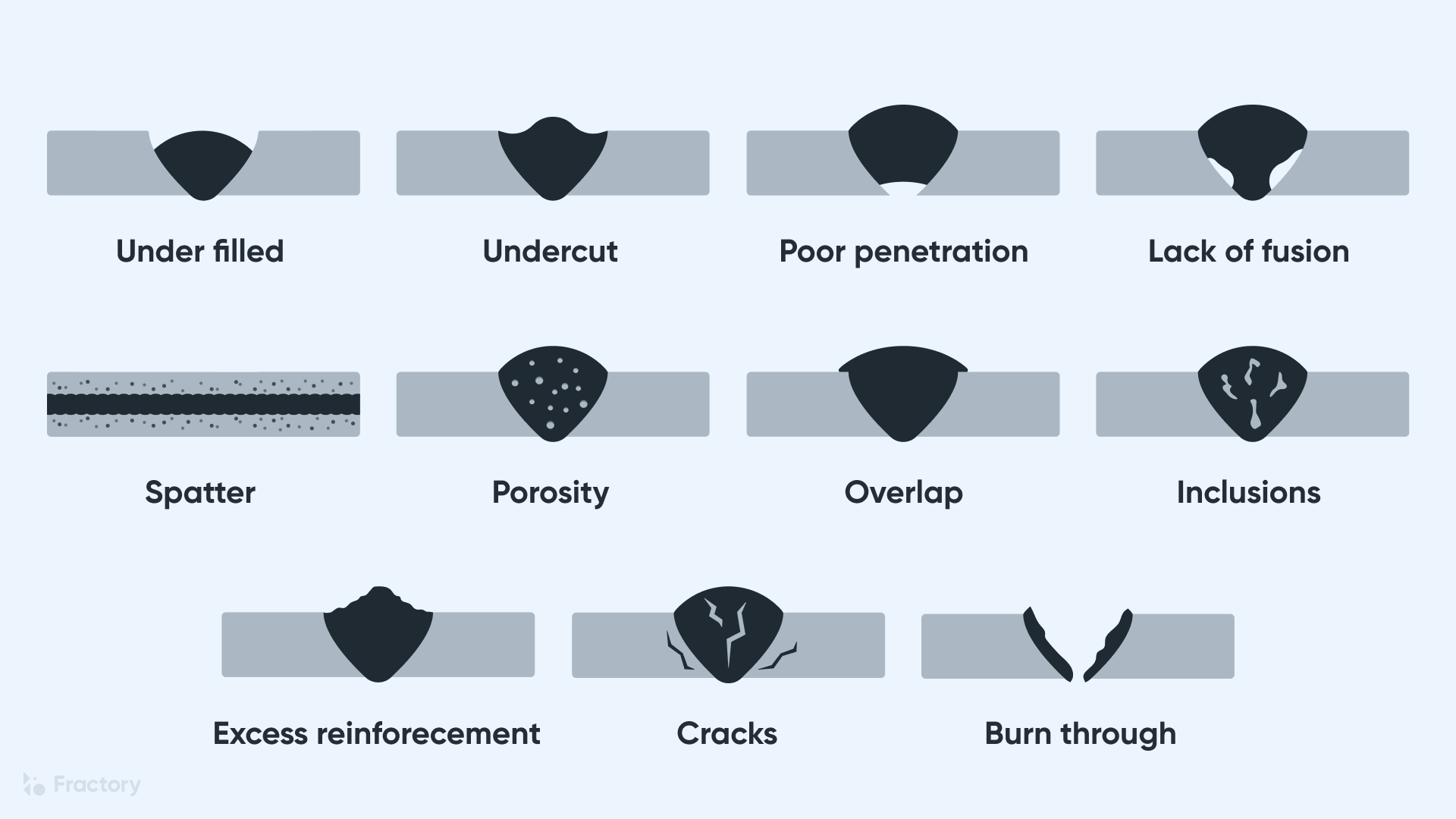
Evaluating and Quality Assurance Steps
Checking procedures are essential to identify and protect against porosity in welding, ensuring the stamina and resilience of the final item. Non-destructive testing approaches such as ultrasonic testing, radiographic screening, and aesthetic assessment are commonly used to determine potential flaws like porosity.
Conducting pre-weld and post-weld examinations is also essential in maintaining top quality control standards. Pre-weld evaluations include verifying the materials, devices setups, and Click Here sanitation of the workspace to stop contamination. Post-weld examinations, on the other hand, evaluate the last weld for any kind of problems, consisting of porosity, and verify that it satisfies defined criteria. Carrying out a detailed quality control plan that includes detailed testing procedures and examinations is paramount to lowering porosity issues and ensuring the general quality of bonded joints.
Conclusion
Finally, porosity in welding can be an usual problem that impacts the top quality of welds. By recognizing the common sources of porosity and applying ideal practices for avoidance, such as correct welding strategies and testing measures, welders can make certain excellent quality and dependable welds. It is vital to prioritize prevention techniques to lessen the event of porosity and keep the integrity of bonded frameworks.
Report this page